— Key levers to reduce CO2 emissions
The two main levers to get to net zero are using low-carbon cement and lime raw materials, and switching to renewable energy sources together with efficiency improvements within factories that manufacture AAC. Two additional levers – circularity and recarbonation – have the potential to make AAC products carbon negative.
Low carbon cement and lime
The use of low-carbon cement and lime binders in the production of AAC would reduce the overall carbon footprint for AAC by 69%. According to industry decarbonisation roadmaps, net-zero cement and lime will be achieved through the use of:
- Carbon capture storage and utilisation (CCS & CCU)
- Low carbon clinker through switching from fossil fuelsto renewable energy to heat kilns
- Alternative binders
- Clinker substitution
- Carbon neutral transport
- Recarbonation6
Switching fuel sources and optimising factories
- Improvements in process control and modernisation of plant equipment
- Replacing fuels such as lignite, coal, heating oil and diesel with fuels with lower CO2 emissions, such as natural gas and biodiesel
- Switching from natural gas to renewable electricity or to hydrogen when available
Decarbonising construction site assembly, and demolition and disposal
downstream in the value chain from AAC
manufacturers. As they decarbonise in line with
Europe’s climate goals, it is expected that 7% of AAC
life-cycle emissions will be removed.
Low emissions transport
Switching to renewable energy
Switching to 100% renewable electricity for ball mills,
offices, warehouses and other facilities would reduce
emissions by 3%.
Circularity
Adopting circular processes for the recycling and reuse of AAC has the potential to reduce emissions by up to 15% initially, then declining to 1% by 2050 as the cement and lime raw materials are decarbonised. For AAC production, up to 20% of the cement and lime raw materials can be replaced through the use of:
- AAC scrap, cracks and leftovers occurring from production
- Leftover AAC cuttings from construction sites
- AAC recovered from building demolition rubble
Recarbonation
Cement-based products absorb CO2 during their lifespan, acting as permanent carbon sinks during the use phase of a building and when it is pulled down and recycled. This process of recarbonation would reduce overall emissions by 43% and has the potential to make AAC products carbon negative. As indicated in the EPD, AAC products can absorb 77 kg CO2 per m3 if complete recarbonation is achieved. Recarbonation reaches around 80% after 50 years and 95% by 80 years. This roadmap assumes a 95% recarbonation rate.
Beyond net zero
Fully implemented, these levers deliver a decarbonisation roadmap for AAC products that reduces emissions from 180 kg to -70 kg of CO2e per m3 by 2050, thereby removing more carbon from the atmosphere than is produced.
Do you want to become a member of EAACA? Contact us!
News

We welcome a new Member – Dongyue Machinery Group
We are pleased to announce that Dongyue Machinery Co, Ltd. has recently joined the association and supports us in our work. Dongyue Machinery Co., Ltd.
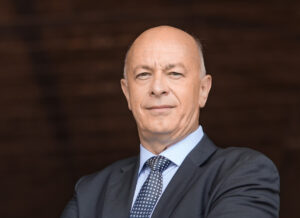
Election Piotr Dauksza
At a recent meeting of the Executive Committee of the European Autoclaved Aerated Concrete Association (EAACA), the Committee unanimously elected Mr Piotr Dauksza as the
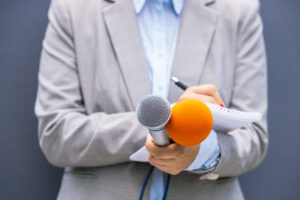
EAACA statement on the current RAAC topic in the UK
Following various media reports on the subject of RAAC in the UK, we as a European association would like to comment on this. Please find